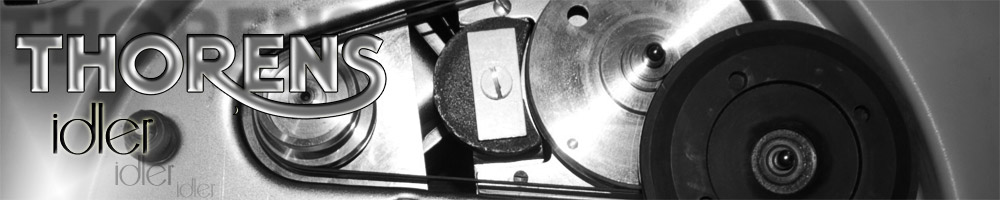 |
THORENS idler Le forum des amoureux des Thorens à galet
|
Nouveau ! THORENS idler est désormais compatible avec l'extension FastNews.kiwi disponible pour votre navigateur. Avec cette extension, vérifiez s'il y a des nouveaux sujets sur ce forum en un clic depuis n'importe quelle page ! Cliquez ici pour en savoir plus.
Sujet précédent :: Sujet suivant |
Auteur |
Message |
El-Mitch Invité
Hors ligne
|
Posté le: Mer 3 Aoû 2011, 18:20 Sujet du message: Nomenclature de la TD 124 |
|
|
Nomenclature extraite de l'article disponible ici : http://thorens.idler.xooit.fr/t116-La-124-dans-la-presse.htm
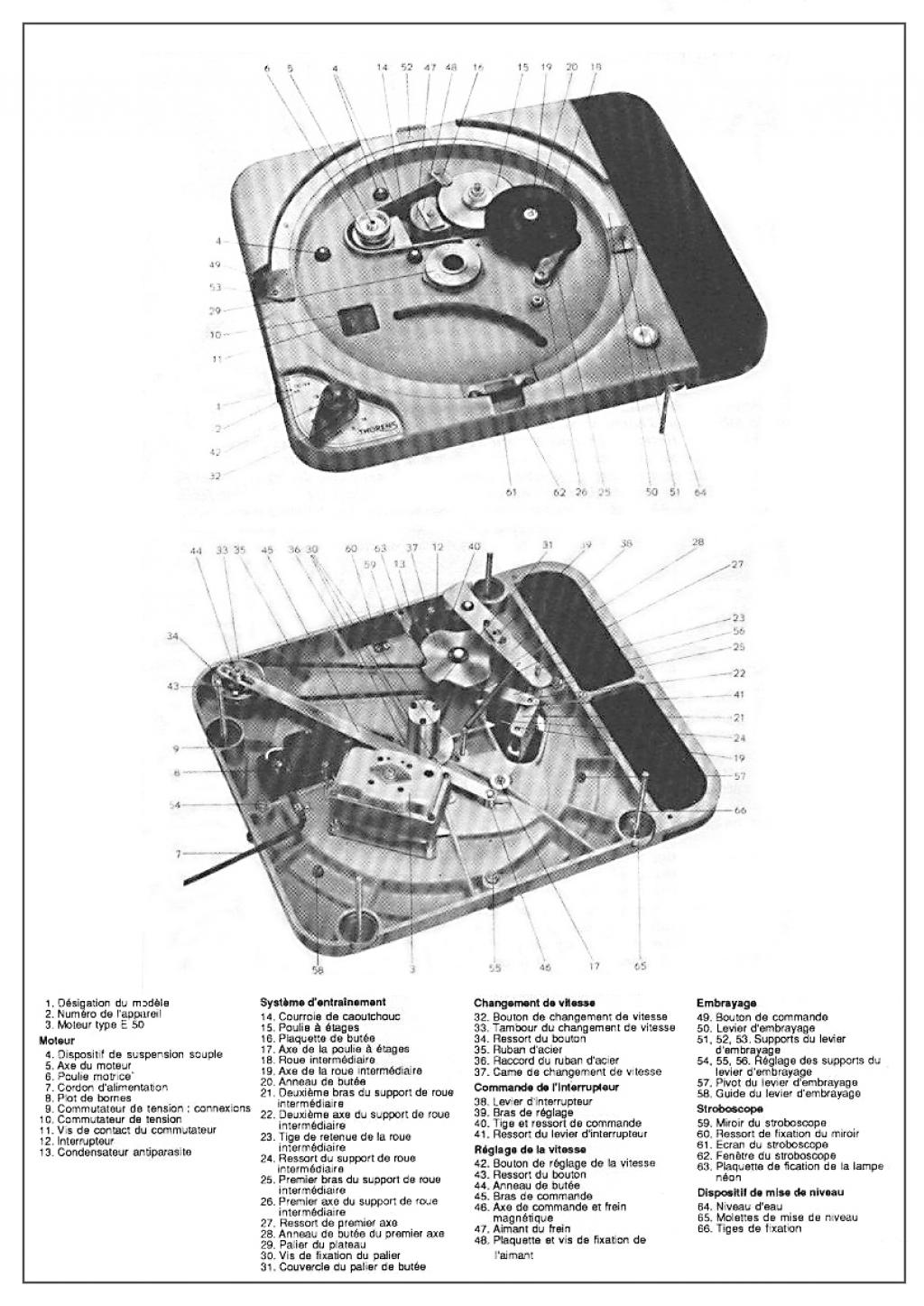
Le format d'origine a été retravaillé pour permettre une impression en A4. |
|
Revenir en haut |
|
 |
Publicité
|
Posté le: Mer 3 Aoû 2011, 18:20 Sujet du message: Publicité |
|
|
|
|
Revenir en haut |
|
 |
Newstalgia Invité
Hors ligne
|
Posté le: Mer 3 Aoû 2011, 18:23 Sujet du message: Nomenclature de la TD 124 |
|
|
Encore un beau sujet de ta part.
Merci Mitch, j'épingle pour la cause
--- Lilian --- |
|
Revenir en haut |
|
 |
papamano .
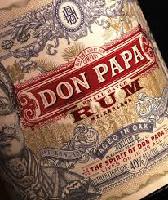 Hors ligne
Inscrit le: 10 Juin 2011 Messages: 4 681
Localisation: 35 dingé  Quel(s) galet(s ): Garrard 301 Ampli: Diafan SE300B Enceintes: Supravox T215SRTF TQWT
|
Posté le: Lun 23 Déc 2013, 10:04 Sujet du message: Nomenclature de la TD 124 |
|
|
http://www.soundfountain.com/amb/td124page.html
 Thorens TD124 Mk II with Ortofon RMG 212 tonearm and Ortofon SPU cartridge on ST 104 base in graduated gray tone as published in Joachim Bung's book "Swiss Precision". Image courtesy Sebastian Schiele, owner of this turntable. | Introduction
| TD-124 and TD-124Mk2 Do you own a Thorens TD 124 or TD 124 Mk2? And do you have the original manual? And maybe you do know a lot about your TD124? So much the better. Maybe this page is not for you. It cannot harm however to look at the images and read some important facts. Many visitors of my website and many Thorens lovers have asked me about the TD124 and TD124Mk2.TD stands for "tourne-disque" which means literally "record turner" in French. The Thorens TD124 has an iron cast platter weighing 4.3 kg, sometimes a bit more. It is driven by a relatively strong 10 Watt motor. (The Garrard 301 has a 16 Watt motor.) The rotation is transmitted via a belt to a stepped pulley. The 4 steps are for the 4 speeds: 16 2/3, 33 1/3, 45 and 78 rpm. The turning of this stepped pulley is transmitted to the inside of the rim of the platter via a rubber wheel. |  | ORTOFON On the left you see the first TD-124 with the long SME 3012 arm and the Ortofon SPU-GT cartridge in an early Ortofon headshell with its particular shape. The shell pictured on the left is a later version which is generally known. | | TD-124 MK2 It is a combination of a belt drive and an idler wheel drive. The TD124 has 4 speeds: 16 2/3, 33 1/3, 45 and 78 RPM. These speeds can be adjusted which is great for people with absolute pitch, for those musicians who want to play along with a recording without having to tune their instruments, and for the playing of shellac records which are not always engraved at 78 RPM but have different speeds up to eighty or even higher RPM. The platter of every TD124 is topped by a light aluminum sub platter. The adopter for 45 RPM discs is integrated. It has a spring and when you push it lightly and turn it to the right it moves up. When you push it lightly down again and turn it to the left, it will lock and stay put. The pattern of the rubber turntable mat consists of closed rings. | Citation: | Thorens TD124 Mk2 and new TP 14 arm
| | TP-14 ARM The TD-124Mk2 has a more modern styled frame and the turntable mat has fewer rings which are interrupted and a new arm, the TP.14, which replaces the earlier BTD-125 arm. But the most important aspect is that the app. 4.395 kg weighing iron platter could be replaced on request by a 3.63 kg. platter of aluminum which of course is non magnetic and thus does not attract a heavy moving coil cartridge with a strong magnet. The TD124mk2 was described by R.L. West in his review for HiFi News of July 1966: "The TD.124 has long been recognized as the Rolls-Royce of transcription motors. It is as solidly made as our Garrard 301 and 401, but has one or two special features of merit. The Garrard takes its drive from a stepped pulley on the motor via a rubber-tyred idler to the turntable. The Thorens interposes a light flat rubber belt between the motor and a separate stepped pulley which drives the idler. This stepped pulley is solid with the main frame, and so prevents any motor vibration , whatever its direction, from reaching the turntable via the drive. (...) Altogether, a very sound machine, still being made just as carefully. (...) The TP.14 arm measurements are most impressive and show Messrs. Thorens are fully awake to the modern need of arms that will behave perfectly down to stylus pressures of below 1 gm if so desired." |  | BEOGRAM 3000 The TD-124Mk2 was soon recognized as one of the most sophisticated transcription turntables available on the market. Both Bang & Olufsen (B&O) from Denmark and Tandberg's Radiofabrik from Norway choose the TD-124 MkII to be incorporated in the top of their product line and the turntable was adorned with their respective logos. At left the Beogram 3000 with B&O tone arm and cartridge. (Edited picture taken from an advertisement in a Dutch record magazine from 1969.) | | 4 SPEEDS This is a picture taken from the instruction manual of an early TD 124. The armboard did not have a black coating yet. When the 16 2/3 speed was proposed in the mid nineteen fifties many manufacturers incorporated the speed into their gramophones and turntables. Right from the beginning the TD 124 also had 16 2/3 rpm which was meant for recordings containing speech and was really not suitable for high fidelity. Note: The aluminum platter which later could be ordered has only 2 stroboscope rings for 16 2/3 and 33 1/3 respectively. It goes without saying that if you have to adjust the downforce of a cartridge when using an iron platter, you have to place the scale not on a record but directly on the rubber mat to get a more exact reading. If you just turn the counterweight to the desired marking when the arm is away from the platter's periphery, or placed on the rest of the lift, you will get a faulty result! | | BELT DRIVE AND IDLER WHEEL The TD-124Mk2 had a more modern look but the combination of a belt driven pulley and a rubber idler wheel of the original TD-124 was of course retained and the heavy platter is turned with the same minimum of wow and practically immeasurable flutter. Rumble values are also exemplary. That is if the bearing functions perfectly well, if the rubber belt is not damaged and not too loose, and if the motor is well de-coupled from the main chassis by three sets of two rubber rings/grommets. The player should be decoupled in some way from its surrounding by means of rubber insulators (originally the mushroom-shaped insulators), or if placed directly on a stand, the stand should have spikes or cones (spikes are preferred). Also the table should be level at all times to function well. See also Turntable Adjustment. | | VERSATILE MACHINE The design, the sturdy build, the specific features no other turntable had, and the precision with which each and every TD-124 was manufactured, made this turntable about the best a man could get. Serious music lovers and audiophiles alike were very fond of this transcription turntable and combined it with tone arms from Ortofon and SME, and with cartridges from Shure and Ortofon. At left an advertisement from 1961. It was published in the April issue of High Fidelity magazine in the US. By that time Thorens products were imported by Elpa Marketing Industries Inc. They also imported Revox tape recorders. An advertisement from 1960 did not mention Elpa Marketing yet. The cost of $99.95 for the TD-124 is amazing, at least measured by non-American standards in that era. The dollar was a strong currency with a high exchange rate. $99.95 for a unit to be built in a cabinet or to be mounted on a plinth are peanuts today. The copywriter's text: "Thorens compensates for variations in house current and recording systems; gives the truest reproduction with all your records, old or new. Adjustment is so fine that records can be used to accompany live vocal and instrumental performances. Swiss precision engineering ensures longer record life, performance to match the finest components you will ever own." The Thorens TD-124 was in the nineteen fifties and sixties what the Technics SP-10Mk3 was for the early nineteen eighties, and to a lesser extent the SP-10 Mk2 for the nineteen seventies - if you consider the variable pitch a necessary feature. It is amazing that many a TD-124 transcription unit is still in use some 50 years after the introduction. It takes some attention and knowledge to keep a TD-124 up and running satisfactorily. The die hards know how to service the mechanism and treat the machine with care, and they eventually substitute one part or another, if necessary: a new idler wheel, a belt, a better spindle and bearing, and maybe a platter. Others just own a TD-124 because they consider it as an antique object and do not bother much about the proper functioning. In any case the paragraphs that follow can give you more insight and ideas in order to fully enjoy the working of this turntable. | CHOOSE ANOTHER TOPIC The Idler Wheel and The Specifications
| VALUES For his review in HiFi News, audio journalist R.L. West meticulously measured the parts and the functioning of the TD-124 Mk2 and compared these data to the measurements on his 4 year old original TD-124. The platter of the Mk2 weighs 8 lb (3.63 Kg). Of course he did not want to weigh the platter of the first TD-124 as this would mean taking the platter off the frame. The spindle is the heart of the matter. Machining it with close tolerance is of the utmost importance. The spindles of the TD-124 and the TD-124 mk2 measured 0.2824 inch and 0.2822 inch respectively. Values for turntable bearing slack measured +/- 0.0015 inch. Wow and flutter was estimated at 0.05 or less than 0.05%. It is unlikely that the polished hard steel spindle will show wear from years of turning. However, the relatively soft sinter bronze bushings can give way to the pressure of the spindle and the turning during decades of service, especially if the machine is not level. | | CENTERING THE PLATTER In case you have bought a new spindle and bearing from Schopper or have a new bearing housing made by a machinist, you will have to insert the spindle (axis) into it. Also if you disconnected the spindle from the platter, you would need a measuring instrument to calibrate the platter the way it was done in the Thorens factory. Naturally the calibrating was done on the inside of the rim, there where the idler wheel touches the platter and where the precise centering is the most effective. In the picture at left it is shown how it was done. If you did separate the spindle from the bearing for whatever reason, see to it that the spindle is completely lowered into the bearing before you place the platter on it. Use a Record Weight to speed things up. But do not force the lowering. After the spindle has completely sunk into the bearing, you carefully place the platter on the spindle and center the platter. At left you see the technician checking and adjusting the precise turning of the green painted platter of the TD-124. The platter of the Mk2 was made of aluminum. The image at left was sent to me by Joachim Bung. It appears in his extensive books Schweizer Präzision and Swiss Precision, with the fascinating story of Thorens, its competitors and its history. Click on the link to know more. | | CARPENTER'S EYE How do you center the platter? Many of you owners have of course found out the best method of checking the correct centering of the platter by using a calibrating instrument. But what if you do not have access to such an instrument? First of all you need a carpenter's eye. Then take a rectangular object, a wooden block or a piece of aluminum, or whatever is suitable, and place it on the armboard. Do not fix the platter to the spindle yet by tightening the screws. Now bring your eyes level with the platter and the rectangular block. Turn the platter slowly with your hand and check at what point the platter is moving inwards and outwards. Shift the platter just a little and check again. The distance (d) should be the same all time. Be patient and take your time. You will certainly succeed in the end. If you are really certain that you have attained the best position of the platter on the spindle, you can gently turn the crews. Do not tighten the first one too much, but give all three the same treatment until you have tightened them well. And then check again of course. | | IDLER WHEEL This drawing is from the original manual of the TD 124 Mk2 and tells you how the adjustments of the idler wheel should be made. If your TD124 works perfectly well and you see to it that the adjustments are right, than there is obviously no need to make changes. The well functioning also depends on other adjustments and the cleaning of some rotating parts. | | CLEAN The speed selector has idle positions in between the speeds. If you do not play, always set the selector in between two speed markings. In this way the idler wheel will not touch the stepped pulley and will not risk to loose a perfect round shape. Clean the periphery (edge) of the wheel with cotton wool and blue methylated spirit. |  | MOUNTING TEMPLATE This image shows the cut out diagram as it accompanies the original manual. If you order a copy of the look alike manual this drawing will be included so you can enlarge it yourself. But you also can order a real size diagram (scroll down for details), if that is more convenient for you. | CHOOSE ANOTHER TOPIC The Spindle and Bearing Housing
| PRECISION BEARING The platter of the TD-124 fits directly on the flange on the top of the spindle and is secured by three screws. The shaft (spindle) is turned and polished to the highest degree of precision. | | IRON AND ALUMINUM PLATTERS The aluminum platter does not have the same shape in the center. It needs an intermediate disc to fill up the original space between flange and platter. The intermediate disc is secured by the three original, large screws. The platter is fixed to this intermediate disc with three smaller screws. | | TEFLON AND SINTER BRONZE This is a drawing to portray the design of the heavy main bearing and shaft without which the turntable does not have the high end quality. The precision turned spindle is polished to the n-th degree and fits with a low tolerance in the 2 sinter bronze sleeves. If the bearing needs maintenance, it should be cleaned with oil. The earliest TD124 turntables had Teflon sleeve bearings (instead of the sinter bronze bushings) and needed to be cleaned with methylated spirit (blue alcohol) if cleaning was necessary. | | BEARING HOUSING If the bearing and the shaft are not handled well, the specifications will not be met. It is of the utmost importance that the housing is hermetically closed at the bottom so that the oil can not leak and the spindle hangs as it were in the oil bath so it is perfectly centered and will turn evenly. | | BALL BEARING The ball was kept in place by a circlip (a washer which is a ring of thin, flexible metal) which clamps into the cavity at the bottom of the shaft. This cavity was greased with dark reddish bearing grease. That was the case with the second hand TD-124 (Mk 1) which I bought in 1978. Later models I bought did not have this grease bearing. | | HERMETICALLY SEALED HOUSING If the oil can leak, the spindle is not supported evenly by the oil and cannot do its job properly. The bearing housing has a base plate at the bottom which must be screwed tightly. In between the housing and the base plate (spindle support pad) a gasket takes care of the complete fitting of the base plate without any leakage. In the drawing it is the thin layer which protrudes at the sides. The original gasket is of a thin material with a brown color. It is a delicate fabric and breaks easily. This gasket can easily be replaced by a gasket that you can cut out of a not too thin but at the same time rather soft transparent sleeve for protection of record covers. You also can use the same sort of transparent plastic, the kind table covers/cloths are made of. This gasket should be larger in diameter than the base plate so that you can trim it to size once the base plate has been screwed on the housing/chamber. When in 1980 a friend and I were developing a turntable with a heavy platter, we initially used TD 124 bearings and spindles. We were thinking of making more tables than just two. So we asked a factory what the price of these parts would be. Recently I found the measurements he wrote down when measuring the parts during our initial conversation. You can see them here. | | MAINTENANCE AND REPLACEMENT Maintenance is important. Clean the bearing and the shaft with oil. Cut a new circular gasket out of the plastic sheet. Put it on the bottom of the still empty housing and with the end of a pair of scissors you make the three holes. Just a small hole will suffice and work better than a large hole. Now put the original, gray, plastic bearing plate (which supports the ball) in the housing. Then put on the plastic gasket with the holes right on the spots were the screws will be inserted. Put the base plate on and insert the 3 screws. Fasten the screws carefully and fasten them tightly. Replace the housing in the chassis of the TD124. Fill it with oil for about 1/3 and gently place the spindle (the platter attached to it) in the shaft and let it slowly settle by itself. Do not force the spindle to go down. The spindle cannot be exchanged for a new one without going to great expense. But if the bearing housing does not support the spindle as it should, if there is some play, it is less costly to have a new bearing housing or sinter bronze bushings made. | CHOOSE ANOTHER TOPIC The Motor and The Suspension
| MOTOR This is what the original motor looks like. This motor was taken of an old machine which could not be restored. One of the shafts for the suspension was broken and the aluminum plate (mounted between pulley and motor) is missing too. A short time after the introduction of the Acoustic Research turntable with the floating (suspended) chassis, designed by Mitch Cotter, Thorens introduced their version of the belt drive turntable with the floating subchassis and named it TD 150 (from which Linn developed their LP12, also inspired when they manufactured the parts for the Ariston sub chassis player). The TD 150 was introduced in 1966. In that same year however, the TD-124 Mk2 was launched but manufactured only for a few years and was eventually replaced by the TD 125 which was produced already from 1968 on. | | PABST AUSSENLAUFER For several years the factory had enough spare parts for the TD124 in stock for replacement and servicing. Despite its sturdy built, the motor of the TD124 could have worn out if the machine was ill treated or accidentally damaged. In 1977 the factory ran out of motors and a new motor was designed especially for the TD124 by the renown manufacturer Papst. This motor was a so called "Aussenlaufer" with the advantage of the flywheel effect. (A similar type was used in the early Acoustical 3000 belt drive turntable, but then with a large capacitor to start the light platter instantly.) While the suspension of the original motor needed 3 grommets, this new Papst motor has longer shafts for the suspension and needs 6 grommets which should be arranged as the image on the left indicates. This should result in a better way to minimize the transmission of vibrations from this motor to the chassis. (Image taken from the original Thorens document.) Check this valuable page for maintenance and repair of the original motor. | | DECOUPLING This picture shows how the rubber isolation rings should be placed in order to attain a maximum isolation. From bottom to top: Hartpapier-Scheibe (hard paper ring), Gummitülle (rubber ring which is inserted in the chassis), Gummitülle (rubber ring), Hartpapierscheibe (hard paper ring), Sprengring (locking ring). Because of the different electrical parameters a new connection diagram was supplied. | | TWO KITS It is possible that you may come across such a fairly new motor. Two different motors were manufactured: kit 3805-200 for 200-240 Volts/50 Hz. and kit 3806-110 for 100-125 Volts/60 Hz. Thorens gave instructions how to take out the old motor and replace the new one, inclusive of a new wiring diagram. | | CONNECTIONS This is the circuit diagram showing how to connect the two different Papst Aussenlaufer motors. The 220 Volt/50 Hz. motor has a capacitor of 0.47 uF/630 Volt plus a resistor with a value in the range of 33 - 82k, 1/2 Watt. The 110 Volt/60 Hz. motor needs a capacitor of 1.5 uF/250 Volt and a resistor with a value in the range 10k - 33k, 1/2 Watt. Legend: SW = switch, Blau = blue, Gelb = yellow, Rot = red, Grün = green, Kondensator = capacitor, Widerstand = resistor. Steve Clarke from The Analog Department was curious about the workings of the Papst motor and built it into the TD-124. He gave a thorough evaluation of the electrical, mechanical and audio related aspects. Though the TD-124 remains an idler wheel turntable, it shows that every aspect of a design contributes to the audible results. Steve noticed a significant difference in sound with the Papst Aussenlaufer motor. This does not necessarily mean that the new motor is in itself a bad design. It means that it should be implemented in a different way or just not in the TD-124. An idler wheel drive is not the same as any idler wheel drive. That is why a Garrard 301, a 401 or a Garrard 4HF do perform in a different way than a Thorens 124, 135, or 111, etc. does. And also a Lenco with the variable speed and pitch adjustment has a different sound. Much of the differences not only depend on the design of the turntable, but also on how their function is optimized in the total system. In this respect it is interesting to know how the Papst Aussenlaufer motor is behaving when mounted in a Thorens TD-124. See Steve Clark's Investigation into the Papst Aussenlaufer. | | MUSHROOMS With four insulators shaped like mushrooms, the chassis can be de-coupled mechanically from the plinth. Here you see the original rubber mushrooms. Visitors of this page often ask me if new ones are available and where to get these. Browse the www or check eBay. | | IMPROVISATION You can of course manufacture some insulators yourself from pieces of rubber tube and top these with small rubber discs and glue these together. Some people just let the chassis rest on the wooden base as I do. But then it is important that the audio rack or cabinet is well de-coupled from its environment by means of spikes or similar gadgets. The turntable has to be level at all times. The horizontal position of the chassis can easily be adjusted by turning the wheels on the threaded bars. | | HORIZONTAL ADJUSTMENT The suspension system of the TD 124 is in essence a simple system, but ingeniously designed. The chassis has threaded holes in which the threaded bars can be screwed. Discs have also threaded holes and can be turned to obtain the best position. By turning the discs clockwise the distance between chassis and plinth is increased. These discs rest on top of the mushrooms. In order to not damage the top of the mushrooms, intermediate rings have to be placed on top of the mushrooms. | CHOOSE ANOTHER TOPIC The Platters and The Clutch
| SIX PADS The main platter has 6 small rubber pads. These are there to support the aluminum top/sub platter in the playing mode. That is when the aluminum top/sub platter is lowered by disconnecting the clutch from it. | | LIGHT ALUMINUM PLATTER It is possible that the clutch does not work correctly. Maybe the aluminum platter is somewhat round on top, overall, or just partially. In that case it will touch the clutch in the up and in the down position. Or the platter may be slightly concave. If it is extremely concave it may be free from the clutch at all times. Either situation has to be corrected. Put the aluminum sub platter on a glass plate and check if the rim is perfect and its edge is supported perfectly well, all around. Even though it is, it is possible that some changes in the surface can be detected. You can check this better if you unscrew the center 45 RPM adapter. (If you are dismantling this center piece, do note exactly what you have done. This makes it easier to reassemble it.) By taking off the mat you can check the surface better. There should not be any part of the aluminum platter that is lower. If the platter's rim and surface needs correction, you should only make changes if you are really sure that you can do that, and if you are certain that the aluminum top platter is the culprit of the malfunctioning of the clutch system. | | THE WORKING OF THE CLUTCH The clutch has the shape of half of a circle. It is a strip which should not have a bend. Check if the clutch is bent or torted. If it is, flatten it. The clutch can of course be adjusted. The drawing (below) shows the functioning of the device. For better understanding you can save the drawing and view it in detail when necessary. There are three screws with a specific shape. If one or two are missing try to find the same or similar ones with the same diameter and thread. Have one end turned by a machinist exactly to the shape of the original screws. In the playing mode, the holes of the clutch fall over the top end of the screws. That means that the clutch is in the down position. By moving the knob of the clutch away from you, the clutch will be lifted and will rest on top of the screws. This means that the aluminum sub platter is resting on the clutch and is lifted also, just enough to let the main platter turn freely underneath, without constraint. If the platter is not turning freely, the locking nuts have to be turned loose and one or more bolts have to be turned as to protrude more. This adjustment is rather delicate. And you only have to make the adjustment if the strip is not bend and only if the former owner has adjusted the bolts unwisely. When playing a record, the sub platter should never touch the clutch. | | THE ORIGINAL DESIGN Some people propagate the use of the TD124 without the aluminum sub-platter. Anybody who is doing this is not using the TD124 as this machine is supposed to function. The clutch action which instantly stops and starts the turning of the sub-platter, should always be used. Repeatedly starting and stopping the machine with the speed selector on the left is not advised. It will use the idler wheel excessively. Putting on and taking of a record while the platter is turning is also not the proper thing to do. Just turn on the machine selecting the speed when you start playing records, and then use the clutch action so you can take off the record and put on the next one. Leave the motor and platter turning, even if you play for hours and hours as I sometimes do. Turn the TD124 off when the concert is over. French designer Jean-Constant Verdier proposes a "modification" of the sub-platter by which a thin sheet of lead is used. He also proposes the use of lead on various parts of the machine. For instance in the armboard in order to eliminate vibrations. I myself do not apply any lead which can clean up the signal by "separating" it from the turntable. You are of course free to follow his philosophy. (Damping the vibrations and letting them die out gradually and not abruptly often is the better way. Od course not over a too long distance/way.) What is the use of having an original TD124 if you are modifying it. On top of it, I am not a propagator of using sheets of lead which make the signal dull. The sole "modification" I propose to you is aimed at improving the support of the record and that is by improving the contact between record and turntable mat. Just cut out 18 small pieces of a heavy magazine cover (about 200 gr. paper) and put 2 together. On 9 spots you divide these twins near the edge of the sub-platter. Even better is to cut out a ring of paper and put it under the mat at the periphery. In this way the rubber turntable mat is slightly heightened at the edge, just enough so to fully support any record. Use a special turntable weight and you will hear the perfect functioning of your TD124 without hardly deviating from the original design. | Maintenance and Adjustments | For effective maintenance there are a few important things you will have to pay attention to. 1. The rubber idler wheel (A), the pulley of the motor (B) and the stepped pulley (C) which transmits the rotation to the idler wheel should be free of dirt and grease. You can use some cotton wool and blue methylated spirit for cleaning. 2. The inside of the platter (D) should be cleaned, as well as the belt (E). Here also you can use methylated spirit. 3. The motor could need some oiling through the hole on the side at the bottom (F). While doing this keep the motor as upright as possible. Also at the top of the motor, the shaft (G) likes a few drops of oil which you apply in between the motor and the aluminum, independent top plate which "separates" the pulley from the actual motor. Do not apply too much and do not grease the belt! 4. You can put one drop of oil on the bearing of the idler wheel (1) and one on the bearing of the 4 speed pulley (2). It may be necessary to clean these spindles and bearings well, especially after many years of service. 5. Some users complain about the fact that the speed is too slow and cannot be adjusted to reach the exact speed, or they complain about the fact that the nominal speed only is effective after more than just 10 minutes. Normally it will take some time for the platter to fully reach the nominal speed. This phenomenon is temperature related and depends on the climate in your country as well as your listening room. (You know that the compliance of your pick up cartridge for instance also depends for a great deal on the room temperature and this does change the character of the sound: more or less openness, rendition of high frequencies, audible distortion, etc.) Right from the start the stroboscope should indicate that the platter is only just a bit slow. If the TD124 does not work right after cleaning and oiling and cleaning of the bearing housing (4), you can adjust the eddy current break (2 &2b) which consists of a magnet in the shape of a half moon (M) and its counterpart (which is part of a circular piece of metal, C). The cleaning tips of belt, platter and pulley are valid for every turntable, be it a Thorens TD124, 125, 160, 166, 145, 126, etc. or any other make of turntable which is driven by a belt or an idler wheel. | Citation: | Adjusting the Eddy Current Brake. Citation: | The large pulley is not shown in this drawing. It conceals device (C). The interaction between (M) and (C) can be varied. This is done by the speed adjustment knob on top of the speed selector (on the left front of the TD124). The more (C) turns towards the magnet, the stronger the breaking action will be and the slower the speed will be. If (C) turns away from (M), the breaking effect will be less and the speed will increase. If you have cleaned all parts and oiled the bearings and still the speed does not reach the exact Rounds Per Minute, you should adjust the magnet. First turn the speed adjustment knob in such a position that C is far away from M. Now loosen the screw of the magnet (M) and move the magnet farther away from (C). Just one or two millimeters could suffice. Reinstall the pulley and the platter carefully and check if there is any improvement and adjust the speed with the speed adjustment knob above the speed selector. If you can not reach the nominal speed and if it is still too slow you have to start all over again and further increase the distance between M and C. If the speed is too fast, than you have gone too far. You have to experiment to find the right position of (M) in relation to (C). Before you start it is wise to turn the speed adjustment knob always in that way that (C) is not direct in front of (M). So you will still have room for more or less breaking when you use the speed adjustment knob. Citation: | Citation: | Citation: | You should always take the utmost care concerning the shaft and the platter. The platter and shaft (spindle) should not be separated as the connection is precisely calibrated in the factory. Although shaft and bearing can easily be damaged when clumsily putting the shaft back into the bearing, it is advised not to separate platter and shaft. Even though the pressure on the base plate and gasket can be very high when putting back the shaft with platter connected into the bearing. In case the platter and the shaft have been separated, do take extreme care to center the platter precisely and screw the platter tight to the shaft (spindle). Always fasten the screws evenly, little by little and check if there is eccentricity before you tighten them completely. The slightest eccentricity should be avoided. The actual position can only be achieved by using a special gauge like the workers in the factory originally used.
|
| | 6. If the belt is noisy you can clean the belt and then turn it inside out and use it that way. A new belt and some other spare parts like the rubber rings and an idler wheel could probably be obtained from Rolf Kelch. If you have a TD124 that works perfectly well, then you are a lucky person. I bought my first TD124 in 1980. Apparently it was not looked after by an expert, so it made quite some noise and had to be attended to attentively. The TD124Mk2 I own now is a perfectly working machine which shows even better specifications than the checklist of Thorens it seems. Wow and flutter are very good and rumble is far better than the -40 dB specified by Thorens originally. You can do a lot to improve the functioning of the TD124. But first of all the rubber rings, belt and idler wheel should be OK. And there are a few people who have set up a forum where hobbyists and lovers of the Thorens TD-124 talk about the virtues, problems, remedies and solutions. A good thing to consult these forums (fora) if you did not find answers to the problems of a malfunctioning on my page. | | | The TD124 Mk II straightforward on the simplest of plinths (I do not use mushrooms!) with Sumiko tonearm from the nineteen nineties and Coral M 8 Moving Coil cartridge with Van den Hul tip. If you do not have a manual for the TD124, SP10 or SME, I can supply brochured copies of these instruction manuals: (Prices in $$$ do vary and will be calculated at the day of your order.) Manuals, Instruction Documents and Templates | Citation: | In due time there will be more info about the Garrard 301 on my pages. Nevertheless you may be interested in the real size mounting template for the Garrard 301 transcription turntable. | Citation: | The cost: $10 / Euro 7. Shipment is $5 / Euro 3.
| | Citation: | Citation: | Service sheets (20 pages DIN A4) with step by step instructions in English for dismantling and assembling SME tonearms Series 2 Improved: $15 / Euro 10 (postage not included). (Prices can vary slightly as the conversion of Euro and USD can change.) Click to order the Manual(s).
| | | Citation: | Owner's and Service Manual of Luxman 2003 Electronic Valve Crossover in English on 24 pages: $25 / Euro 20 (postage not included). (Prices can vary slightly as the conversion rate of Euro and USD can change.) The Luxman 2003 Electronic Valve Crossover with 8 x 12AU7 is a fine unit and can certainly be built by the amateur with knowledge about electronics and experience in building components. This Owner's and Service Manual contains all schematic diagrams and values of resisters and capacitors. It also contains images of the 4 circuit boards (3 for the channels and 1 for the power supply). As an extra I have edited the images so they can be used for etching the circuit boards in case you would like to overhaul your unit or build a unit from scratch.. I have also added extra information about the unit and how to make the prints for the selection of the crossover frequencies. The manual also explains the functioning of the x-over: selecting frequencies, polarity of amplifiers, polarity of speaker units in relation to the chosen slopes of 6 or 12 dB. Click to order the Luxman Valve Crossover Manual. TOP OF PAGE | |
Citation: | SP-10MK2 OWNER'S MANUAL The brochured, exact copy of the Technics SP-10 Mk2 Owner's Manual in English on DIN A4. The cost: $7 / Euro 5 Shipment is not included.
| | | Citation: | SP-10 REAL SIZE MOUNTING TEMPLATE INSTALLATION DIAGRAM MONTAGE PLAN SCHEMA D'INSTALLATION INSTALLATIONSDIAGRAM MONTAGE-DIAGRAM Large real size copy of the original mounting template. The cost: $12 / Euro 9. Shipment is not included. I will add a real size template for the construction of the clamp/shipping bracket. For that you can use a sheet of aluminum.
| | | The Thorens Direct Drive Turntables | DIRECT DRIVE In the 1970's the direct drive turntable became popular. Panasonic had developed their SP-10 with variable pitch. Direct drive means that the platter is resting on the spindle of the motor. In fact the platter is in place of the pulley. In this case a very heavy, slow turning motor is necessary instead of a small motor which turns at high speed as in the modern belt drive turntables. The strength of the direct drive motor (its accuracy and its torque) can be used completely while eliminating any transmission by intermediate parts: idler wheel, belt, pulleys. Since motors do not turn smoothly but rotate in steps (the more poles the smoother the rotation), the turning has to be regulated electronically, has to be smoothed out, in order to achieve a continuous and even turning. TD 524 Thorens applied the direct drive technique when designing their semi professional studio motor deck, the TD 524 (the "24" reminiscing the TD 124). EMT had a similar turntable. It was their answer to the success of the Technics direct drive turntables ever since the launch in 1970 of the SP-10 and the further development of the SP-10 mk2 and mkiii turntables. | | FIRST DIRECT DRIVE PATENT IN 1928 Many thought that direct drive was a new technique, but it existed long before the LP was introduced. Thorens developed an electrical direct drive motor way back in the nineteen twenties. Thorens applied for a patent for this direct drive turntable motor, tourne disque in French. On the document is written: "TD à commande directe". It was issued by the "Bureau fédéral de la propriété intellectuelle" (Federal Office of Intellectual Ownership) in Switzerland, on June 21, 1929. The ins and outs were described in the "Exposé d'Invention" (Description of the Invention). Thorens however refused to use a direct drive motor in the music lover's turntables in those days. At the time the technique was probably too expensive to make it work to perfection. | | THORENS DD IN THE EARLY 1950s It is not common knowledge that Thorens produced a series of direct drive turntables in the early nineteen fifties: CD 43 Record Changer, CBA-83 Automatic Player, CB-33P Manual Player and E-53PA Turntable (Motor Deck). They all had the E 53 N motor. | | Citation: | - You can manually adjust the speed for "exact pitch" on 78, 45 and 33-1/3 rpm records. Furthermore, speed is not affected by heat or load conditions! - | | | BEFORE THE TD 124 WAS DEVELOPED The message in the advertisement (above, left) published in the June 1954 issue of High Fidelity Magazine reads: Rubber belts, pulleys, idler wheels and other wearable elements of friction-drive turntables contribute to unwanted noise and pitch variation. There are non of these in a Thorens. This and similar advertisements were the answer to the immediate and vast success of the Garrard 301 turntable launched in 1954. At left the specifications of the Garrard 301 grease bearing finished in gray hammeroid It was assistant editor J. Gordon Holt (then 25 years old, later founder of Stereophile) who reviewed the Garrard 301 machine in High Fidelity Magazine of October 1955. His conclusion: "Though semiprofessional in price, we feel the Garrard 301 rates a professional rating on a basis of quality and performance and would be willing to bet that it would continue to give dependable service for a considerable time." The technical features and mechanical aspects of the table were reviewed. No subjective evaluation of the performance was included as this was not done in those days. | Thorens E 53 N direct drive motor. | COMPETITION The picture at left shows part of the innards of the Thorens E 53 N direct drive motor as used in the E 53 PA and other Thorens direct drive turntables. This is not what we regard as a direct drive motor today. It is obvious that the E 53 N motor was a further development of the type of standard motor used in the electrical turntables in the 78 rpm shellac era with the transmission of the rotation via tooth wheels and worm wheels. Thorens boasted of a -48 dB rumble value, 0.1 % for flutter and less than 0.3 % wow for this motor. The image is part of the advertisement for the E 53 PA transcription unit and other Thorens direct drive turntables printed in High Fidelity Magazine, October 1956. It is clear that the success of the Garrard 301 Grease Bearing Transcription Unit forced Thorens to abandon this concept and to develop their TD-124 with belt and idler wheel in order to obtain values for wow and flutter matching those of the Garrard 301: wow 0.2 %, flutter less than 0.5 %. It took some three years to develop the TD 124. | A Note about the Value of other Thorens Turntables. First check attentively if the turntable is complete. Beware for instance of a TD124 offered without the aluminum sub platter. Do not buy it. (Unless you absolutely have to.) You should know that it is difficult to get a second hand aluminum sub platter which is not bent. No sub platter means playing records by starting and stopping the main platter by means of the speed selector, or by putting the record on and lifting it up while the platter spins. And that can only mean intensive wear on the idler wheel and belt and record. | The TD 125 (which superseded the TD 124 and TD 124 Mk2) uses the belt drive/swinging chassis principle which was originally designed by Mitch Cotter from Acoustic Research. The TD 125 is a very good turntable. The TD 125 Mkii has different (improved) electronics and is tops. Both the TD 125 and 125 Mkii were highly admired for their mechanical and sonic qualities. The Td 126 was a further development. The TD 126 MkIII however got a lower rating if compared to the earlier TD 125, to the simpler TD 160, TD 126 MkI and MkII, because of the use of a tachometer (like in the TD 105 and TD 110). In the TD 126 MkIV this method was abandoned and the Mk IV has better stability. | At the time the TD125 was launched the TD124 Mkii was still being sold for a while. At the same time the TD150 was introduced. It had like the TD124 and TD125 a wooden armboard which is advantageous for mounting all sorts of arms. This feature was later copied by Linn, but abandoned by Thorens in the TD 160, 166 and subsequent types. Could be that the armboard material would make a difference in sound and if the board was changed by the owner, the basic characteristic of the turntable, as it was designed by Thorens, could change. Like the AR turntable, the TD150 is also designed with the swinging/floating sub chassis and belt drive system which was used later by Ariston, and then copied by Linn in the development of the LP 12. The TD150 is a good vintage turntable also because it has this interchangeable arm board. | The TD 160 and 166 were derived from the TD 150. The TD 160 has high end quality, despite the fact that it does not have the wooden armboard any longer. The TD160 is well designed and uses an aluminum/zinc inner platter and practically any 10" tonearm can be mounted, though only if the owner has some skill. TD 166 is a cheaper model because its inner platter is of a plastic compound which does not have the same mechanical and acoustic properties, and it has a the simplest of Thorens tone arm. The TD 160 has value and more if it is offered with a quality tonearm. Never expect the TD-160 to be sounding like a TD-160, because it is not high end. And do not believe the slogan on eBay indicating that the TD-166 is a "very sought after record player". | My advice: go for quality: TD124, TD124Mk2, TD-125, TD-126 Mk1, 2 and 4 and TD-160 all have value; and of course the Reference and the Prestige. Personally I would not opt for a TD-105, TD-110, TD-145/147 and TD166. These are nice tables, but you should not pay high prices for these models. The Thorens TD126 Mk3 did not deliver the same performance of the Mk1 and Mk2. The motor had a tachometer and corrected any variation in the speed of the platter, but in fact the corrections came always too late. | As regards to the TD 126 Mk3 the HIFI-CHOICE review of 1978 stated that "Wow and flutter on steady state measured very well, but there still remain some doubts over the servo response under transient conditions." This anomaly can be minimized by adding a bit of foam plastic to the existing foam inside the springs. It is strange that the Thorens-technicians did not stick to methods and designs which had proven to be right in the 125 and early 126 machines. Obviously the Mk3 was an answer to the Japanese direct drive tables which boasted of a minimal deviation of the nominal speed. Thorens had much to fear from the Direct Drive players. Thorens returned to the earlier synchronous motor and electronic regulation as used in the TD125 and the earlier TD126 editions when they marketed the TD126Mk4. The Mk3 always can be made to sound better by removing the flimsy bottom plate and constructing a heavy wooden base plate of plywood. And if the turntable has been leveled precisely, the reservation of HIFI-CHOICE may in general disappear or be minimized. | Arm Boards and Tonearms | If you cannot fit the arm onto the existing TD 124 armboard that you have, because either the hole is too large or the board is not large enough (in case you want to use a 12" tone arm), then the best thing to do is to copy the armboard on paper (trace around the armboard with a pencil and take the exact measurements). Look for a similar sort of chipboard which was used by Thorens, sand it and spray paint the top and sides several times. If you are not too handy or want the arm board to be manufactured professionally, you can go to a carpenter and have it made. Of course you can experiment with other materials like tropical wood, plywood, etc. Avoid ebony and other hard tropical woods and avoid acrylic. It is possible that birch plywood is too hard for your system. | | You may try meranti, or yet another softer wood. The experimentation is well worth the effort and then you can decide. Most offers on the web for arm boards are cosmetic versions and have not been listened to. (The same goes for plinths. Some are very expensive, but what about the synergy with the TD124 in your system?) The measurements of the armboard are: TOP SIDE: Width: 72.5 mm, Length: 320 mm. REVERSE SIDE: Width: 66 mm. The thickness is 11.8 mm (inclusive of thin layers of paint). You can save and print these scans. TD 124 Armboard. If there is no arm board, then you can make one yourself. | | My advice: do not use acrylic arm boards because of the thickness you have to use. Acrylic does not have the desired sound properties Like glass it equalizes the fine details already in the lower end of the sound spectrum. Hence they cannot be followed by their harmonics as desired. Transient response is also less. You can hear that when an orchestra suddenly plays a complex and very dynamic passage. Also do not use MDF because that has an uneven sound pattern (as you can hear in most DIY loudspeaker systems The lower mids are somewhat emphasized. And unevenness influences the upper harmonics.) | | If you want to use a 12" arm then the armboard has to be larger of course. Make sure the pivot of the arm is mounted in such a way that it does not touch the diecast frame with the 3 holes. For 12" arms you can choose between many shapes: large boards, tapered boards, slender boards with a minimum of weight, etc. When you buy a new tone arm you should pay attention to the right distance between the pivot of the tonearm and the spindle and the right distance in millimeters between the needle tip and the spindle (overhang). Specifications and instructions are given in the manual of the tone arm you have. If you want more info on how to adjust and calibrate arm and cartridge, just  If you buy a second hand tonearm pay attention to its condition. Check the wiring with a voltmeter: make contact with each separate wire at the front (head shell) and the outgoing lead at the arm base Sometimes the arm can be rewired. Most of the time it is very difficult to do this. If you do not have enough experience, leave it to an expert. If there is none available, leave the arm as is. | | The most important aspect of the tonearm however is the bearing. There should be no play in the bearing. You can check this when the arm is mounted on a turntable: hold the headshell and pull it in the horizontal plane towards you. When the arm is not mounted you take the pivot in the left hand and with your right hand you pull the headshell away from your left hand. Be sure to put the counterweight on. If there is play then the arm moves at the pivot (base) and you should not buy that arm. In some cases you can adjust the bearing, but most of the time that also is a tricky business. Always avoid play in the bearing, but do not adjust the bearing to tight so that the arm has difficulty in moving up and down (vertical plane) and left to right (horizontal plane). The TD-127 was the last edition from a system which was developed from the TD125 and TD125Mk2. But it did not have the same stability as the 125 and 125Mk2. Nevertheless it is a good turntable if you put a quality tonearm on it. If the chassis of the turntable swings too much you could add a bit of plastic foam to the inside of the springs, or renew the existing foam (take the same amount). Never put too much. Too much will make the sound less transparent. The chassis (platter and arm) should always be level (completely horizontal in all planes, from left to right and from the back to the front). | Thorens TD224 Record Changer Image edited by R.A.B. (taken from the original TD 224 leaflet). | On the basis of the TD124 (but using the smaller bearing of the TD135) the TD 224 was developed. It is a record changer which was by its ingenious and complex design a remarkable machine. The TD 224 was a record changer which did not have the anomaly of the common record changer: the always changing angle under which the grove would be read (vertical tracking angle which changes according to how many records are stacked). | | 1. The records to be played are stacked at left. 7", 10" and 12" records can be played. 2. The first record on top of the stack is being grabbed by the arm and transported to the platter. 3. The platter starts turning and the tonearm reads the signal. Thus the 224 was playing records just like any 'ordinary' turntable would. 4. When the record has been played, it is grabbed again and put on a lower platform for played records. 5. The last picture shows that all records have been played. There is no record left and the mechanism stops. | | The TD224 had the same arm as the TD124 except for some modifications at the arm base. This turntable does not have a clutch. The switch at the front is the main control. A push to the right is for the Start or Reject function. The left position is for manual use. The speed lever at the left can be left standing in any position, as the idler is not dependent of its position. When the TD 224 shuts off power after all the records have been played, the idler wheel disengages automatically. Note: On the TD 135 this knob is for activating and disabling automatic stop at the end of the record. Stop can be automatic, or by holding the switch in front in Stop position as long as the platter is turning. If the platter is not turning, the motor will not stop. The main switch engages/disengages the idler wheel, Trond Kjetil Holst from Norway told me. You can visit Trond Kjetil Holst's Website. On the TD 224 the window for reading the stroboscope was positioned to the left. This was done for practical and not for esthetic reasons. | | The mechanism of the TD224 is quite complex because the motor has to drive the platter as well as move the changer arm. It can be seen that the double motor pulley (for 50 and 60 Hz.), the belt and the stepped 4 speed pulley are the same as in the TD124. There are however two idler wheels which are both driven by the motor. The idler wheel at right drives the platter. The other one activates the complex mechanism which consists of several transmission wheels which move the changer arm. These wheels take up a lot of space. That is why the shaft and bearing housing of the TD224 are not the same as used in the TD124. In the TD224 the shaft and bearing housing of the smaller TD135 player are used. The complexity of the construction can be seen in the second picture. A system of arms, mechanical relays and springs are activated at the end of the record when the tonearm is lifted up. When the record is taken off and a new record is put on the platter, the tonearm automatically is moved to the beginning of the record and the music starts again. The purpose of this elaborate construction was to keep records as mint as possible and also -which was very important- to keep the position of the cartridge with cantilever and tip always at the same angle to the record. This was unique. In all the other changers available on the market the growing stack of records gradually changed the Vertical Tracking Angle. You can see the TD 224 working in a video on Carsten's site. | | | In order to be able to grip a record, the spindles of the collector and of the distributor pads, had a rectangular shape leaving two small openings in to which the lifting 'clamps' (grapples) could go and grab the record at the spindle hole. While the record was lifted and transported, the label was pushed against the undersite of the pad. In this way the record was well balanced and kept horizontal until it was released. When I lived for a couple of years in France, in Paris, in the nineteen sixties, friends and I often visited the jazz clubs and the special bars where jazz records were played. 'La Payotte' was one of those bars. Another one was 'Le Crocodile'. In 'Le Crocodile' a Thorens TD 224 changed from Sonny Rollins to Duke Ellington, Jackie MacClean, Cecil Taylor, Miles Davis and Dave Brubeck (to name a few of the favorites at the time). And they all sounded very well because of the Thorens TD224. It was for a guy who was interested in good music and in the technicalities of the sojund reproduction not only a joy for the ear, but also for the eye. |  | © Rudolf A. Bruil - Page first published on the www August 2001.
____________________________________________________________________________________________________ un bon fauteuil,du jazz,un cigare,un rhum vieux,des amis.......je suis le roi du monde member of the L70 F.U.C sylvain |
|
Revenir en haut |
|
 |
pierrot62 .
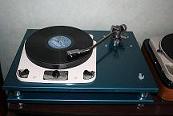 Hors ligne
Inscrit le: 18 Aoû 2011 Messages: 1 215
Localisation: Calais  Quel(s) galet(s ): TD 124 MK1 , GARRARD 301 Ampli: Cochet AL2 Ampli Live sound, p
|
Posté le: Lun 23 Déc 2013, 10:19 Sujet du message: Nomenclature de la TD 124 |
|
|
Bravo Sylvain ,ça c'est de la doc 
____________________________________________________________________________________________________ Pierrot |
|
Revenir en haut |
|
 |
papamano .
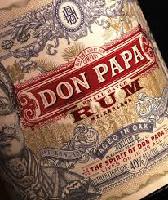 Hors ligne
Inscrit le: 10 Juin 2011 Messages: 4 681
Localisation: 35 dingé  Quel(s) galet(s ): Garrard 301 Ampli: Diafan SE300B Enceintes: Supravox T215SRTF TQWT
|
Posté le: Lun 23 Déc 2013, 10:37 Sujet du message: Nomenclature de la TD 124 |
|
|
je savais pas que Thorens avait fait du Direct Drive style Rek-O-Cut

____________________________________________________________________________________________________ un bon fauteuil,du jazz,un cigare,un rhum vieux,des amis.......je suis le roi du monde member of the L70 F.U.C sylvain |
|
Revenir en haut |
|
 |
Tourne disque .
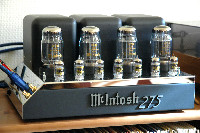 Hors ligne
Inscrit le: 24 Déc 2011 Messages: 1 716
Localisation: france 
|
|
Revenir en haut |
|
 |
Contenu Sponsorisé
|
Posté le: Aujourd’hui à 14:31 Sujet du message: Nomenclature de la TD 124 |
|
|
|
|
Revenir en haut |
|
 |
|
|